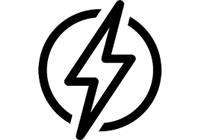
Manufacturers understand that there will be a lot of quality control and PCB testing involved in the PCB manufacture process. Many quality tests are done to guarantee that a design can be manufactured at scale and with good quality, although most of this happens behind the scenes and without the designer's knowledge. During prototyping, other crucial tests, such as PCB functional testing and IC programming, are usually the responsibility of a designer, and these tests will be folded into production when producing at scale.
Whatever degree of testing and inspection you require, it's critical to identify the fundamental test requirements for your design and convey them to your manufacturer. Read our list of PCB testing requirements if this is your first time going from prototype to high-volume manufacturing so you know what to anticipate.
PCB Testing In Manufacturing
Several PCB testing processes are carried out during the fabrication and assembly process. These are used to evaluate the quality and yield of bare PCBs, as well as to guarantee that a design has passed through assembly without errors. Additionally, during manufacturing/assembly, electrical testing will be done and compared to the design netlist.
The testing of prototype designs does not cease when they are manufactured. After receiving the boards, the design team should do board bring-up testing and functional testing before finishing the design. Some of these measures may need to be automated when you expand to hundreds or millions of boards to ensure high throughput and quality.
During production, a minimal set of mechanical tests and inspections are done to validate the fabrication process and assure the board will be installed reliably.
These tests can be performed to assess whether there is a quality issue with the manufacturing process, whether rework processes are necessary, or whether there is a design flaw that causes the test to fail. Additional tests, such as MIL-STD vibration tests, NEMA/NFPA/FAA fire safety tests, thermal shock tests, HALT/HASS tests, burn-in testing, environmental tests, UL safety tests, and other product/industry-specific tests, may be required in addition to these fundamental tests. If your company is unable to execute these more extensive tests, there are speciality testing businesses that will thoroughly certify new items.
PCB Electrical Testing During the Manufacturing Process
Electrical testing is also done throughout the production process to look for any flaws, impedance aberrations, or soldering residues
In-circuit testing checks for open and short circuits, as well as particular voltage and current values on test points. A test fixture is sometimes used to measure a specific waveform. In addition, power-on or power-off electrical tests can be utilized to check for component problems using specific components or test locations.
ROSE (resistance of solvent extract) test: This conductivity test is used to check for any remaining solder flux residue. TDR stands for time domain reflectometry. In single-ended and differential traces, this test is performed to determine impedance. This can be done on a test coupon or a test board with a fixture connected. To completely evaluate signal integrity, some additional de-embedding and analysis is required.
Electrical testing: To check for flaws, flying probe testers probe particular spots on the PCB.
flying probe testing
Functional Testing of PCBs
Functional testing for electronics covers a wide number of scenarios, many of which are aimed at assuring that the device delivers the expected user experience and end functionalities. Rather than being the job of the manufacturer, this is the responsibility of the design team at the prototype process. Your manufacturer's role is to provide you with a PCBA that electrically matches the design data you provide them; functional verification is not their responsibility.
If the design fails to generate the desired functional test results, it is the designer's responsibility to troubleshoot and debug the design to find the source of the problem. To find the sources of any issues, the designer or test engineer may need to manually collect some electrical data, experiment with firmware, and retrace problems through the design. Once these have been identified, they may be addressed in the next design version and, ideally, integrated as test requirements when the product is scaled up.
You should define special electrical, thermal, or mechanical testing for your manufacturer if you're transitioning to larger volume and your product's functioning or standards compliance necessitates them. Speak with them early to ensure that they understand your requirements and that they have the ability to automate these tests in order to assure product quality. These activities require time up front, but you'll have peace of mind knowing that every conceivable flaw has been foreseen in the design.
- Comments(10)

**
May 11.2024, 21:54:45

M****Lue
Apr 21.2024, 06:22:55

M****Lue
Apr 21.2024, 06:21:03

M****Lue
Apr 19.2024, 11:46:05

M****Lue
Apr 19.2024, 11:46:05
M****Ali
Apr 06.2024, 18:21:13

m****lam
Apr 04.2024, 20:54:11

O****oki
Apr 04.2024, 11:15:51

m****lam
Mar 31.2024, 20:09:08
