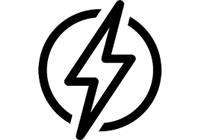
Introduction
The V-CUT is the PCB manufacturer make a partition slot after build the PCB as the customer's requirements. Most of the customers will choose to panelize printed circuit boards and split it by there own. The “V” partition line can facilitate the customer to split the panel.
Consideration of V-Cutting
The reason why PCB manufacturers usually depanelize printed circuit board before shipping is that they have to consider multiple factors, such as increasing the production capability of SMT (surface mount) equipment and reducing the bottleneck of equipment operation. Second, the PCB manufacturer needs to balance the utilization rate of its board to reduce costs. Third, because of the different design of the printed circuit board, in the PCB manufacturing factory, it usually needs to go through many different processes.
Most of the printed circuit boards are FR4 (epoxy-based) or aluminum-based, so it is not very realistic to use manual hands to directly divide the PCB. Even if you want to split it, you should v-cut the PCB in manufacturing factory.
Compared to hand breaking, using V-CUT depanel machine to split the edge of the printed circuit board process is more stable. Meanwhile, more PCB manufacturers adopt to V-cut.
Difficulties in V-Cutting
Though V-CUT is designed to deal with a variety of square products, there are still difficulties. For example, when it needs space in between V-cut area, engineers will still require personnel to manually break (such problems are very common in many designs).
Assembled printed circuit board after the tungsten steel knife will cause the rest part of PCB fall in the transmission belt, and easy to cause the product hit some fragile parts such as MLCC (ceramic capacitors) or some sensors. In this case, to some products, the V-cut machine should be modify.
As the name implies, v-cut is v-shaped. It often relies on the shape of the V for positioning. Usually when workers operate, the PCB jumps out of the tool because of the lack of accurate positioning, and the product is scrapped. While the current products are thinner and lower, they are often the hardest hit areas for cutting and scrapping.
Therefore, the V-CUT process often requires customers and manufacturers to work for the final high-quality PCB.
Router - Another Way for De-panelization
Because the current electronic products are no longer simply like the past as square or some connectors are designed in the board rules, including wearable products or medical products CT MRI, etc., There are a large number of soft and hard combination of circuit boards, so Router become particularly important.
The Benefit of Router
1. Router can make non-linear segmentation which is different from the V-CUT.
2. Motor-driven rotary head division, according to the computer programming of the circuit board or electronic components of the stress is small, not easy to cause damage to the solder joints.
3. Not to the problem of the existence of human-operated V-CUT, leading to cut injury circuit (provided that the production of effective positioning tooling).
4. The life of the tool can be effectively controlled.
5. From the environmental point of view for the PCB dust collection effect is good, no occupational health effects on personnel.
6. High consistency of processed products with complete independent equipment operation (but requires effective debugging and maintenance).
Conclusion
To optimize panel area and increase the productivity of the SMT assembly process, PCB penalization is necessary. V-cut or Tab route is created for depanelizing the final PCB, taking into account the design, cost, and other variables. If you want high-quality panelized PCBs, you should engage with a seasoned PCB manufacturer like PCBGOGO who is familiar with the panel requirements.
- Comments(7)

**
Dec 26.2023, 00:30:05

C****pez
Nov 27.2023, 17:19:27

**
Nov 27.2023, 16:33:17

**
Nov 27.2023, 16:32:05

L****llo
Nov 21.2023, 18:08:58

S****ard
Nov 20.2023, 11:09:33
A****van
Nov 01.2023, 16:38:19